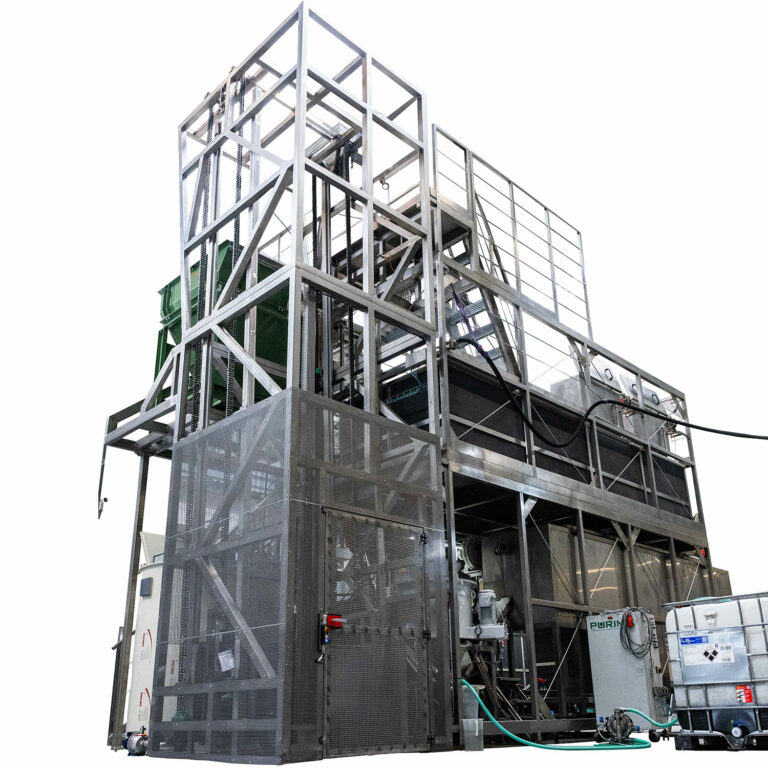
Industrial cleaning powerhouse for chip recycling
The stuff that quality is made of: metal swarf is an important and expensive recyclable material that is reused in the manufacture of fittings in a wide range of industries. However, the swarf must be cleaned for this purpose as part of the manufacturing process.